
Overall design plan for the automated production line for hot forging of nuts
发布时间:
2025-07-10
The common hot forging nut production line generally consists of frequency conversion furnace coils for heating, sizing, pre-forming processing, and forming processing. Currently, the hot forging nut processing process mostly involves three presses performing three stages of forging at three different stations, and the raw materials are inspected and transported by manual operation on the presses. This process is inefficient and has high labor costs. Based on the aim of reducing costs, this article introduces the development direction of the automatic production line device for hot forging nuts.
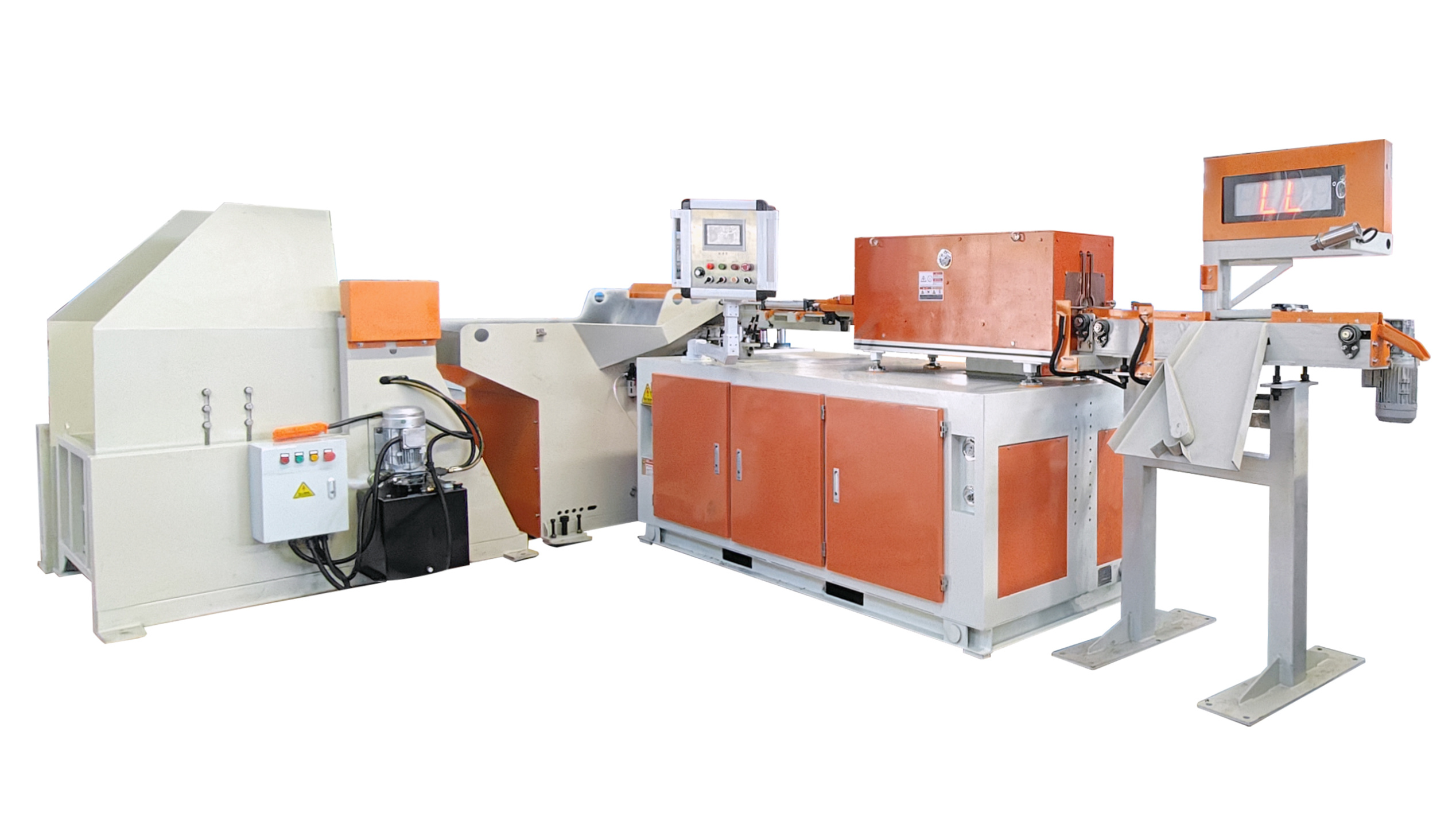
The automated production line for hot forging nuts is mainly composed of an automatic untying device, an automatic hole alignment conveying device, a cutting machine, a lifting device, an automatic feeding device, a medium-frequency heating device, an automatic discharging device, an automatic feeding device and a nut hot forging machine, etc.
The working procedure is as follows: The automatic unbolting device automatically unbolts the bundled bars and successively pushes the bars to the automatic alignment conveying device. The automatic alignment conveying device automatically aligns the bars with the inlet of the cutting machine and completes the automatic cutting by the cutting machine. The cut bar sections are lifted by the automatic lifting device and poured into the automatic feeding device. The automatic feeding device lifts, sorts and conveys the bar sections to the heating coil controlled by the medium-frequency furnace. After heating, they are transported to the automatic feeding device. At this time, the automatic feeding device sends the hot bar sections to various stations of the nut hot forging machine for forging. The forged nut blanks are sent out by the automatic discharging device.
Related News